Greener route to widely used industrial material
5 May 2022
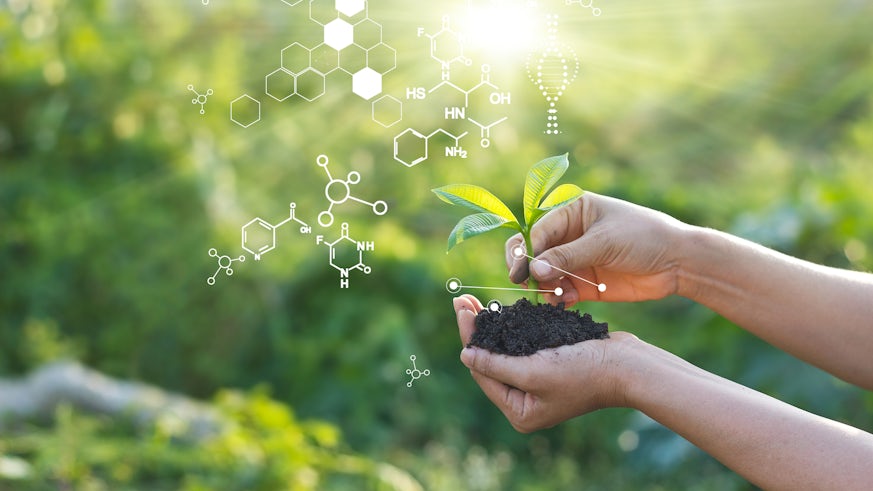
Scientists from Cardiff University have taken a step towards a greener, more sustainable way of creating a plastic material found in a range of items from toothbrushes and guitar strings to medical implants, construction materials and car parts.
In a new paper published today in the journal Science, the team report a brand-new method of creating cyclohexanone oxime – a pre-cursor to the plastic material Nylon-6 which is a key construction material used in the automotive, aircraft, electronic, clothing and medical industries.
It is estimated that global production of Nylon-6 is expected to reach around 9m tonnes a year by 2024, prompting scientists to search for greener and more sustainable ways of producing cyclohexanone oxime.
Currently, cyclohexanone oxime is produced industrially through a process involving hydrogen peroxide (H2O2), ammonia (NH3) and a catalyst called titanosilicate-1 (TS-1).
The H2O2 used in this chemical process, as well as many others, is produced elsewhere and needs to be shipped in before it can be used in the chemical reaction.
This is a costly and carbon-intensive process that also necessitates the shipping of highly concentrated H2O2 to the end-user prior to dilution, which effectively wastes the large amounts of energy used during concentration.
Similarly, the stabilising agents often used to increase the shelf-life of H2O2 can limit reactor lifetime and often they need to be removed before arriving at a final product, leading to further economic and environmental costs.
To address this issue, the team has devised a method where H2O2 is synthesised in-situ from dilute streams of hydrogen and oxygen, using a catalyst consisting of gold-palladium (AuPd) nanoparticles that are either directly loaded on to the TS-1 or on a secondary carrier.
Nanoparticles, which measure roughly between 1 to 100 nanometres, are extremely useful materials to use as catalysts due to their large surface area-to-volume ratio compared to bulk materials.
The method was performed in conditions previously thought to be extremely detrimental to H2O2 production and can produce yields of cyclohexanone oxime comparable to those seen in current commercial processes, while avoiding the major drawbacks associated with commercial H2O2.
Furthermore, the team were able to demonstrate the versatility of this approach by producing a range of other industrially important chemicals, which themselves have wide ranging applications.
Lead author of the study Dr Richard Lewis, from the Max Planck–Cardiff Centre on the Fundamentals of Heterogeneous Catalysis, based at the Cardiff Catalysis Institute, said: “This work represents a positive first step towards more sustainable selective chemical transformations and has the potential to supersede the current industrial route to cyclohexanone oxime.
“The generation of H2O2 through this new approach could be used in a wide-range of other industrial applications that are currently dependent on the use of TS-1 and H2O2, potentially representing a sea change in industrial oxidation chemistry.
“This is a clear demonstration that through academic and industrial collaboration, significant improvements on current state-of-the-art technologies can be made, leading to significant cost savings and a reduction in greenhouse gas emissions from a major industrial process.”
The study was led by Cardiff University in collaboration with UBE Corporation, Shanghai Jiao Tong University, Research Complex at Harwell, University of Bath and Lehigh University.