Researchers to create “chatty factories” of the future
27 November 2017
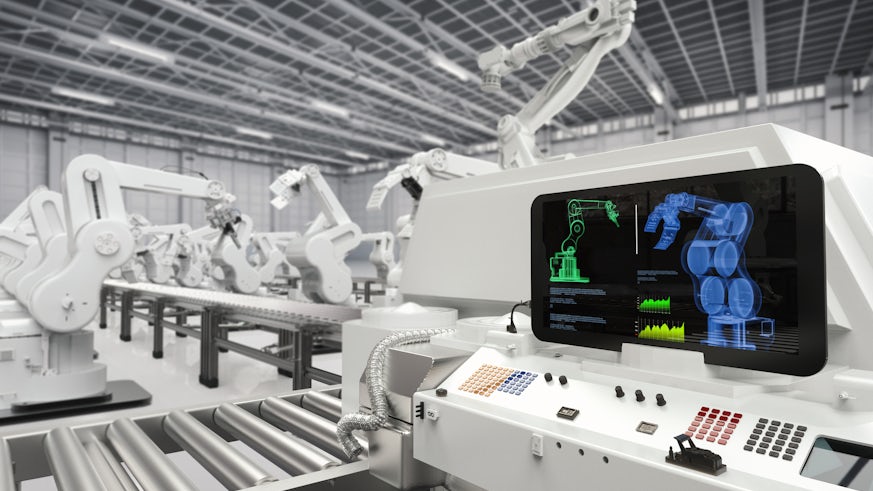
New £1.5m project will create system in which products can “talk” to the factory floor in order to transform the modern manufacturing process
Imagine a bike helmet that could send a text message to your phone to tell you that a crack had developed underneath the surface of the helmet.
Simultaneously, imagine this information being instantly pinged back to the manufacturers of the bike helmet so they could almost immediately adjust their processes and improve the next batch of bike helmets on the production line.
This idea of people, products and production processes being intrinsically connected is the vision of a brand new £1.5m project that is being led by scientists at Cardiff University.
The three-year project is aiming to take advantage of the rapid growth of the ‘Internet of Things’, in which everyday items have the ability to “talk” to each other and transmit massive amounts of useable data.
By embedding sensors into products that we use in our daily lives, the goal is to create one seamless process that is capable of continuously changing products based on data from the users.
The project, dubbed “Chatty Factories”, could potentially save significant amounts of time and money spent on consumer research, concept design, prototyping and manual labour on the factory floor, as well as providing ideas for brand new products.

“The current manufacturing process is limited by the inability to quickly and continuously refine product design based on a consumer’s experience, and simultaneously re-skill the human and robotic processes on the factory floor."
“If manufacturers are creating high-end bikes worth thousands of pounds, but they are not being used as they are intended, how do we update the fabrication issues and reshuffle the factory floor between shifts, telling human and robot workers how to alter their duties within minutes?
“Our new method will enable manufacturers to sense the experience of the product, building something based on its actual use rather than its intended use.”
The idea of using real-time data from sensors has been rolled out extensively in the aircraft industry, specifically for monitoring the performance of jet engines; however, the data is used to tweak the optimisation of an existing product, rather than generate new ones.
Over the next three years the project team will be developing artificial intelligence to process the large amounts of data, exploring ways in which sensors can be embedded into products, developing robots to re-skill the factory floors and making sure all of the interconnected products and processes are able to understand one another.
Each strand of research will be underpinned by the latest advances in cybersecurity, ensuring the creation of safe, secure and robust processes.
The project has been funded by the UK’s Engineering and Physical Sciences Research Council and also involves scientists from the University of Edinburgh, University of Nottingham, Lancaster University and Bath Spa University.
Share this story
The School is research-led with a reputation for excellent teaching and internationally accomplished research activities.