Additive manufacturing laboratories
Mae'r cynnwys hwn ar gael yn Saesneg yn unig.
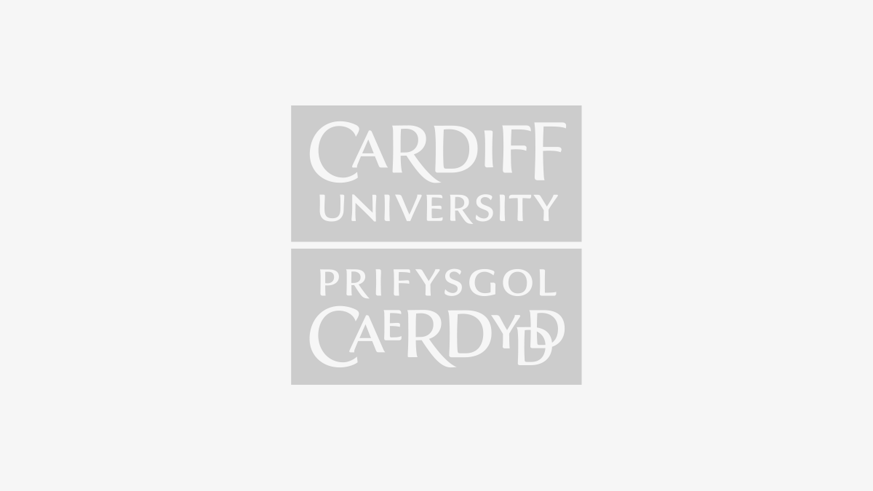
The Additive Manufacturing Laboratory at the School of Engineering has a recognised established track record of additive manufacturing research and development in metal sintering and polymers since the mid-1990s, and has a proud history of collaboration with business and industry.
This research area has a proud history of collaboration with business and industry. Over the past six years we’ve worked with more than 630 companies, ranging from small design houses to leading manufacturers and innovators such as Dunlop, Orangebox, Northern Automotive and Dyson. We work in many substrates, such as medical grade materials, enabling innovation in sectors from healthcare, through high value manufacturing, to the creative industries.
Technical features:
A Renishaw AM 250 was added to the facility in 2015, and metal Additive Manufacturing has since become the focus of AM research, covering both material and process development. Complete ownership of the powder bed fusion (PBF) system allows full exploitation of features to investigate the parameters, novel parameters, and manufacturing capabilities of the machine.
In addition to PBF part manufacturing, the laboratories are equipped with:
- Nabertherm N41/H Furnace, including Argon shielding equipment, which can be used to heat treat PBF samples’ post-processing operations.
- EDM and bead blasting equipment for part removal and cleaning.
- Facilities for sifting and mixing powders (including ball milling and Speedmixer) are also available within the department, together with a Malvern Mastersizer 3000 for particle size analysis of metal and composite powders.
Research Highlights:
AM research at Cardiff School of Engineering covers a broad scope of activities, including:
- Novel materials development: One of the major research challenges facing AM is developing materials which can be successfully processed using PBF to produce desired final properties. Cardiff School of Engineering has investigated the optimisation of PBF parameters for manufacturing of non-standard metal powders for engineering applications, and developed opportunities for using PBF to produce metal matrix nanocomposites, adding small volumes of ceramic and other non-metal nanoparticles to the metal powder before melting, to enhance the characteristics of the final component.
- Process capability management: Improving the understanding of the PBF manufacturing process by developing an approach which can provide quantitative evidence of process integrity, necessary to underpin the acceptance of PBF components. An assessment technique that can be applied to manage the process capability of PBF machines has been established, which will enable more effective process set-up and control.
- Design for AM: Use of advances modelling and simulation techniques, such as finite element analysis and topology optimisation to maximise the benefits of AM processes in producing the final component. Examples include the development of new lightweight tooling design for aerospace manufacturing, and the introduction of AM to reduce manufacturing lead times in flexible manufacturing systems.
- In-process monitoring for additive manufacturing: The Tribology and Performance of Machines, Structures and Materials Research Group are developing Acoustic Emission techniques for detecting part failure during manufacture in metal AM systems, focussing on the location and characterisation of component failure using advanced signal processing techniques with the ultimate aim of creating a control process for AM systems.
- High-frequency engineering for additive manufacturing: Cardiff’s Centre for High Frequency Engineering is involved with numerous research projects with Renishaw. These include investigating RF and microwave methods for powder bed heating, capable of reducing thermal stress and improving part integrity, research into the characterisation of AM powders by analysing microwave absorption, and the optimisation of metal AM components through post-processing to optimise the application of AM in manufacturing microwave and mm-wave devices.
Recent industrial collaborations include Renishaw, Airbus, Safran and Continental Teves. The lab is currently supporting 7 ongoing PhDs, combining both industrial and research council funded projects.
Equipment
The following equipment is available within our suite of laboratories:
Renishaw AM250 | Currently used for research purposes. | |
HiQ | Currently produces parts in Polyamide, unfilled and glass filled. | |
DTM, model 2500 plus | Currently used for research purposes. | |
Stereo Lithography | 3D Systems, model 5000 | 500mm square x 600mm high build space. Material is a mimic of ABS. |
Stereo Lithography | 3D Systems, model 3500 | 350mm square X 400mm high build space. Material is mimic of polyproplene. |
Thermojet | Used for pattern making. | |
AGIE Excellent | Produces features and components down to 20 microns |
Practical applications
The research carried out in the field of advanced manufacturing at the School of Engineering is driven by practical applications in industry. Our focus is on the development of sustainable products and efficient and sustainable manufacturing processes. We have worked with many companies and organisations to assist them to improve their manufacturing processes and products. The laboratories are able to create extremely high quality components for prototypes, rapid tools and industry-ready production parts.